Highlights
- E-waste contains valuable rare earth elements (REEs) essential for high-tech applications, with hard disk drives and fluorescent lamps having the highest concentrations.
- Conventional REE recovery methods include physical separation, hydrometallurgy, and pyrometallurgy, while emerging green technologies offer improved sustainability and efficiency.
- Future research should focus on developing eco-friendly processes, optimizing technology integration, and conducting life cycle assessments for sustainable REE recovery from e-waste.
Electronic waste (e-waste) contains valuable rare earth elements (REEs) essential for various high-tech applications, making their recovery crucial for sustainable resource management. Rare Earth Exchange has covered research tapping into innovative ways to potentially more efficiently and effectively treat recycled products to tap into and separate rare earth elements. An imperative key due to China’s stronghold on9 rare earth element processing, owning about 90% of the total market. This review provides an overview of the occurrence of REEs in e-waste introducing both conventional and emerging green technologies for their recovery. Conventional methods include physical separation, hydrometallurgy, and pyrometallurgy, while innovative approaches such as bioleaching, supercritical fluid extraction, ionic liquid extraction, and lanmodulin-derived peptides offer improved environmental sustainability and efficiency.
The Chinese authors include case studies on the extraction of REEs from waste permanent magnets and fluorescent powders, pointing to the specific processes involved.
But more research is needed the authors point out, emphaising a focus on developing eco-friendly leaching agents, separation materials, and process optimization to enhance the overall sustainability and efficiency of REE recovery from e-waste, addressing both resource recovery and environmental concerns effectively.
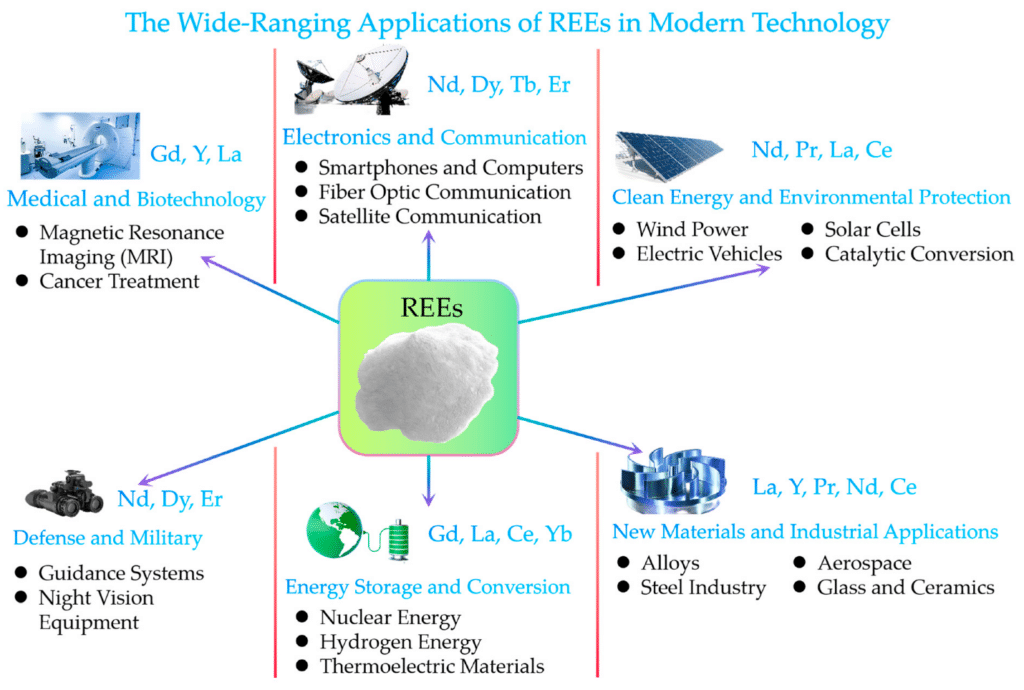
As demonstrated in the table below, hard disk drives and fluorescent lamps contain the highest concentrations of REEs, particularly neodymium, dysprosium, yttrium, and europium. The permanent magnets in hard disk drives, such as NdFeB (neodymium–iron–boron) magnets, are the primary source of neodymium and dysprosium [**13**,22 (opens in a new tab)]. The phosphors in fluorescent lamps, on the other hand, are rich in yttrium and europium [22 (opens in a new tab),23 (opens in a new tab)]. Smartphones, computers, and televisions also contain various REEs, although at lower concentrations compared to hard disk drives and fluorescent lamps. The REEs in these devices are mainly found in components such as screens, speakers, and vibration motors
Table 1. Typical REE content in various types of e-waste.
E-Waste Type | Main Components | REEs Present | Concentration (ppm) | Ref. |
---|---|---|---|---|
Hard disk drives | Permanent magnets | Nd, Dy, Pr | 2500–15,000 | [13 (opens in a new tab),22 (opens in a new tab)] |
Fluorescent lamps | Phosphors | Y, Eu, Ce, Tb, La | 1000–20,000 | [22 (opens in a new tab),23 (opens in a new tab)] |
Smartphones | Screens, speakers, vibration motors | La, Ce, Pr, Nd, Sm, Eu, Gd, Tb, Dy, Y | 10–1000 | [23 (opens in a new tab)] |
Computers | Printed circuit boards, hard disk drives, speakers | La, Ce, Pr, Nd, Sm, Eu, Gd, Tb, Dy, Y | 10–1000 | [24 (opens in a new tab)] |
Televisions | Screens, speakers | Y, Eu, Tb | 10–100 | [13 (opens in a new tab),24 (opens in a new tab)] |
An overview of the sources, impacts, and recovery options for rare earth elements in electronic waste.
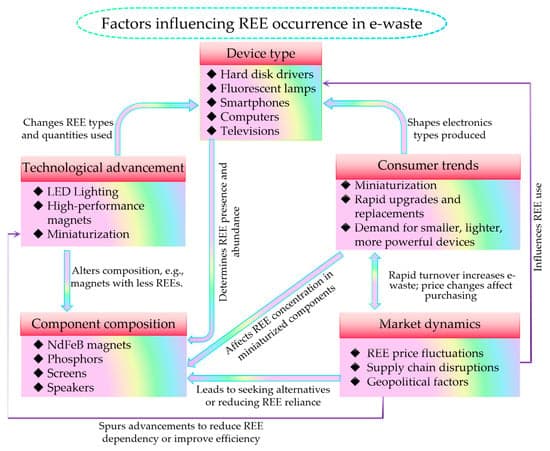
Overview of REE recovery methods from e-waste: physical separation, hydrometallurgical extraction, pyrometallurgical extraction, and emerging green technologies.
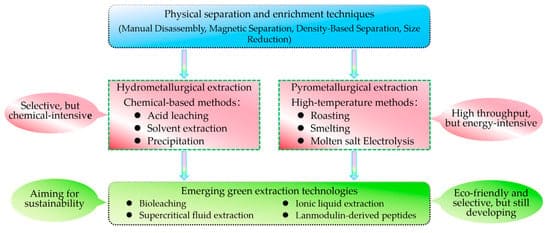
Overview of physical separation techniques for REE recovery from E-waste.
Technique | Principle | Advantages | Applications | Efficiency/Considerations | Ref. |
---|---|---|---|---|---|
Manual Disassembly | Hand separation of REE-containing components | High precision, suitable for high-value components | Recovery of NdFeB magnets from hard disk drives | Labor-intensive but effective for valuable parts | [47 (opens in a new tab)] |
Magnetic Separation | Separation based on magnetic properties | Efficient separation of magnetic materials | Isolation of NdFeB magnets from other e-waste materials | Most effective for REE-containing magnetic materials | [48 (opens in a new tab)] |
Density-Based Separation | Separation based on density differences | Can separate components with different densities | Gravity separation or flotation | Suitable for materials with significant density differences | [49 (opens in a new tab)] |
Size Reduction and Sieving | Particle size reduction and classification by size | Improves efficiency of subsequent processing | Liberation and classification of REE-containing materials | Prepares materials for chemical processing, enhancing efficiency | [50 (opens in a new tab)] |
Overview of hydrometallurgical techniques for REE extraction from e-waste.
Technique | Principle | Advantages | Applications | Ref. |
---|---|---|---|---|
Acid Leaching | Dissolution of REEs using acidic solutions | High leaching efficiency, selectivity | Extraction of REEs from NdFeB magnets, fluorescent phosphors | [58 (opens in a new tab),59 (opens in a new tab)] |
Solvent Extraction | Selective separation of REEs using organic extractants | High purity, efficient separation of individual REEs | Purification of leach solutions containing multiple REEs | [59 (opens in a new tab),60 (opens in a new tab)] |
Precipitation | Formation of solid REE compounds by pH adjustment or addition of precipitating agents | Simple, cost-effective | Recovery of REEs as oxalates, carbonates, or hydroxides | [61 (opens in a new tab),62 (opens in a new tab)] |
Overview of pyrometallurgical techniques for REE recovery from e-waste.
Technique | Principle | Advantages | Applications | Ref. |
---|---|---|---|---|
Molten salt electrolysis | Electrochemical extraction of REEs using high-temperature molten salts | Efficient separation of REEs from complex matrices | Recovery of REEs as oxalates, carbonates, or hydroxides | [78 (opens in a new tab)] |
Roasting | High-temperature conversion of REE compounds to oxides | Improves leaching efficiency, enables selective recovery | Treatment of REE phosphors and oxides | [79 (opens in a new tab)] |
Smelting | Melting e-waste at high temperatures to concentrate REEs in molten phase | Enables recovery from metallic components, high throughput | Purification of leach solutions containing multiple REEs | [75 (opens in a new tab),81 (opens in a new tab)] |
Schematic illustration of the bioleaching process for REE recovery from e-waste.
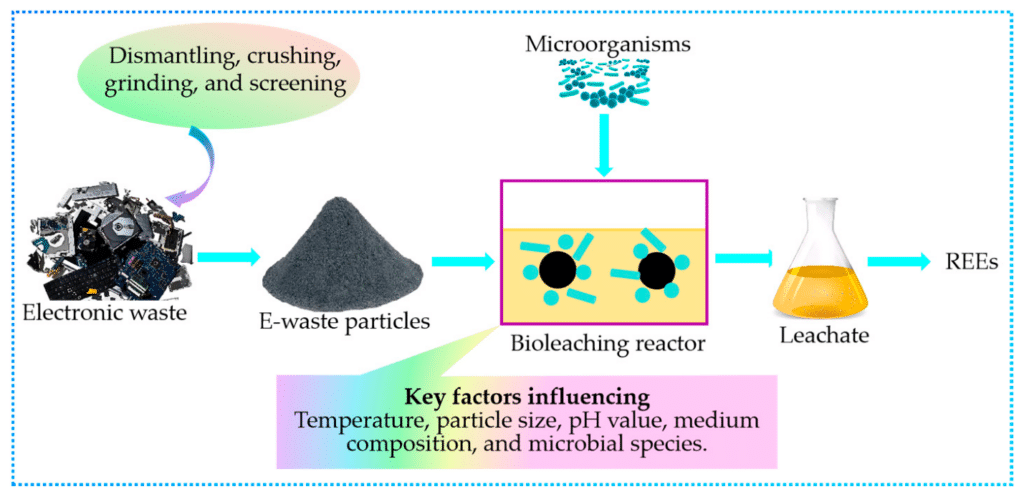
Schematic diagram of supercritical fluid extraction of rare earth elements from e-waste.
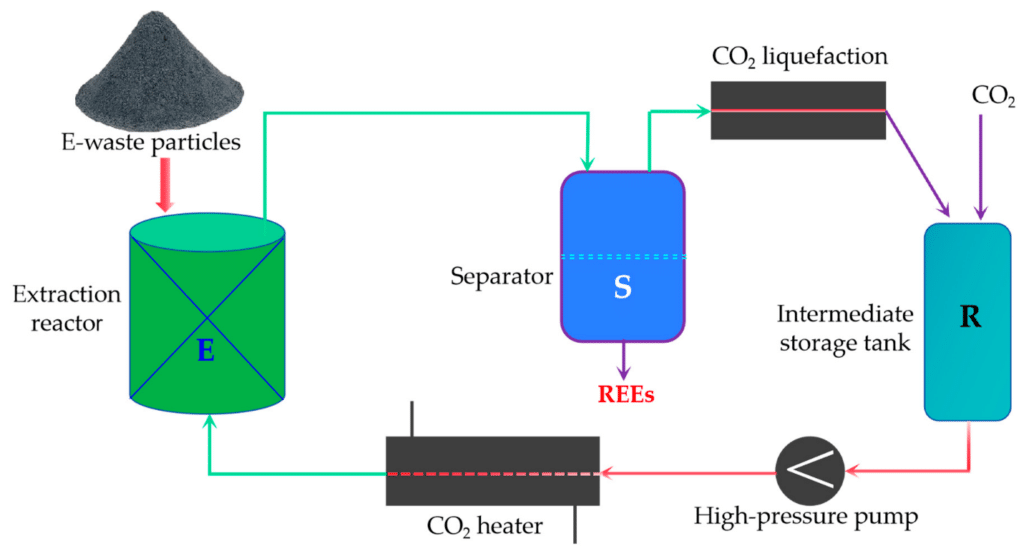
Schematic diagram of ionic liquid extraction of rare earth elements from e-waste.
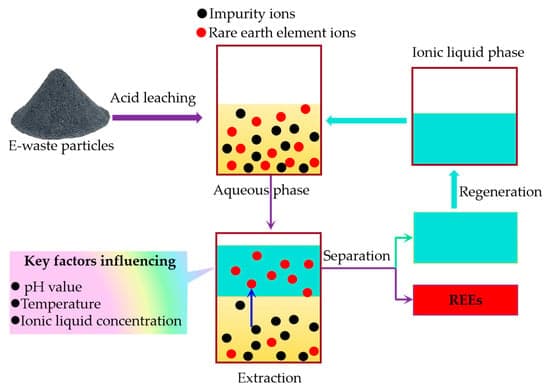
Schematic of the MNP-LanM biosorption process for selective REE recovery. Reprinted with permission from Ye et al. [102 (opens in a new tab)]. Copyright 2023 Royal Society of Chemistry.
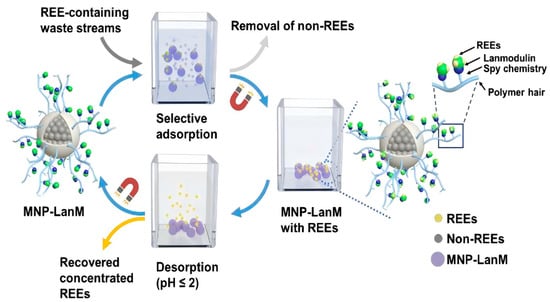
Efficiency varies widely depending on specific REEs, source material, and leaching conditions.
Comparison of REE recovery methods from e-waste.
Method | Recovery/% | Recovered Form | Env. Impact | Energy Use | Cost-Effectiveness | Pros/Cons | Ref. |
---|---|---|---|---|---|---|---|
Traditional hydrometallurgy | 80–99% | Metal salts, pure metals | Moderate chemical waste | Moderate | High | +High efficiency −Chemical-intensive | [104 (opens in a new tab)] |
Bioleaching | 40–90%* | Metal ions in solution | Low | Low | Moderate | +Eco-friendly −Time-consuming | [105 (opens in a new tab)] |
Supercritical fluid extraction | 80–95% | Metal complexes | Low waste generation | High | Moderate | +High purity −High pressure required | [106 (opens in a new tab)] |
Ionic liquid extraction | 85–98% | Metal ions in ionic liquid | Low volatility, reusable | Low | High initial cost | +Selective extraction −High cost of ionic liquids | [107 (opens in a new tab)] |
Pyrometallurgy | 80–95% | Metal alloys, pure metals | High energy use, emissions | Very high | Moderate | +High throughput −High energy use | [27 (opens in a new tab)] |
Schematic diagram of REE recovery technology optimization and integration.
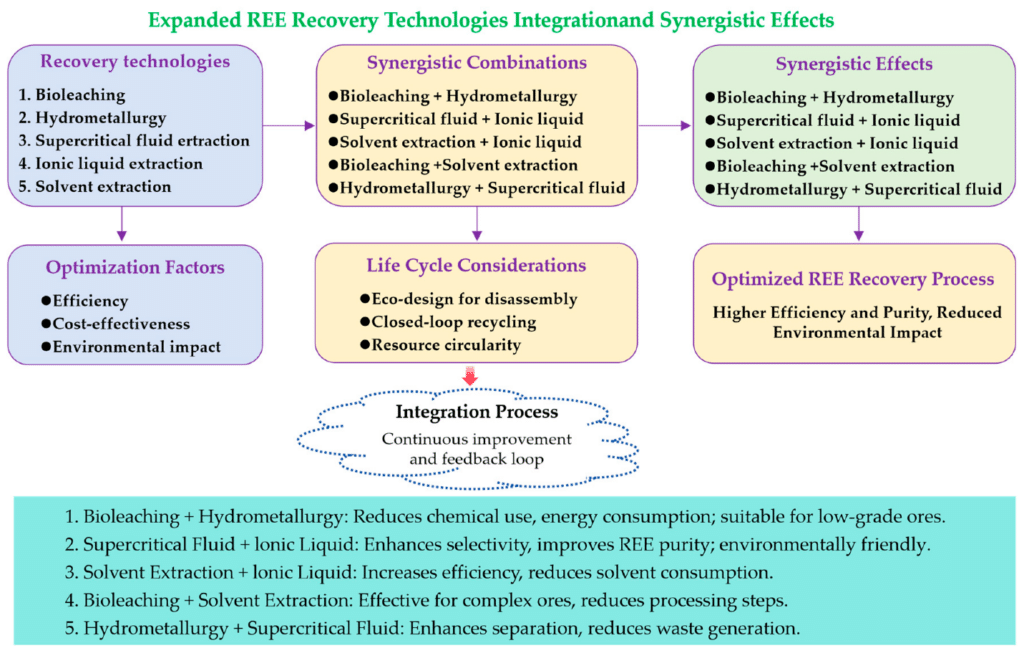
Sources, distribution, and environmental impacts of REEs in e-waste and their recycling process
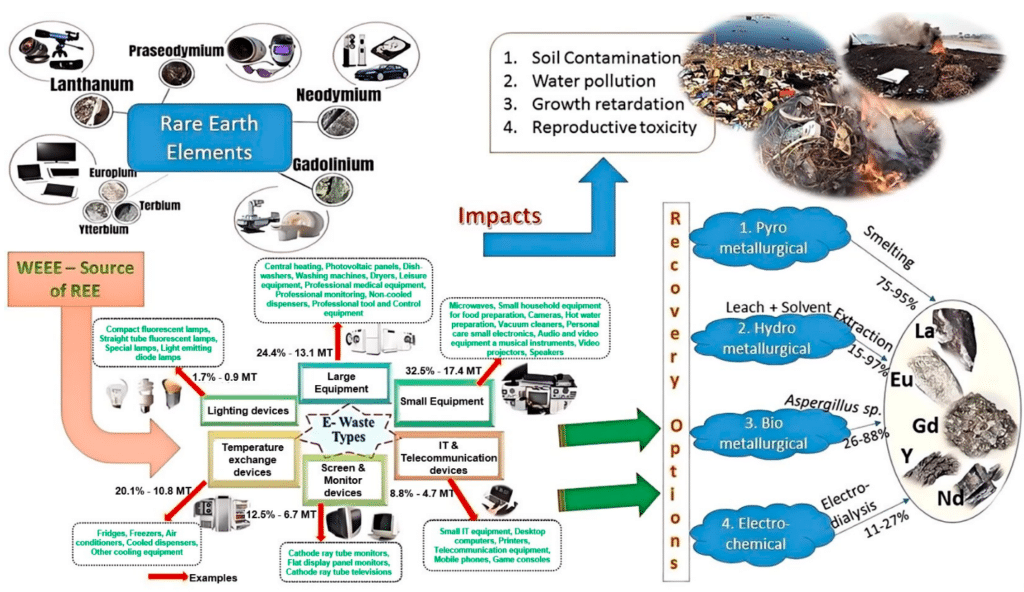
Summary
The authors of this review shine some light on the immense potential of e-waste as a secondary source of rare earth elements, with a particular focus on waste permanent magnets and fluorescent powders.
Offering an in-depth analysis of the factors influencing REE distribution in e-waste, the group present a systematic evaluation of various extraction techniques.
Considerable challenges must be faced, from technical barriers and economic viability issues to environmental sustainability considerations. There is no denying that recycling objectives with e-waste is fraught with risks.
Only a multi-faceted approach can help overcome such challenges.
Encompassing the establishment of robust recovery systems and regulations, the optimization and integration of extraction technologies, and the synergetic development of resource utilization and environmental protection.
What’s on the Research Agenda
Advanced research in this domain should focus on the development of eco-friendly and efficient recovery processes while also considering the entire life cycle of REEs, app part of an effort to minimize environmental burdens.
According to the authors:
“Specifically, we recommend investigating novel extraction technologies that balance efficiency with sustainability, optimizing the integration of various recovery methods for more holistic approaches, and conducting comprehensive life cycle assessments of REE recovery processes.”
What are the Ingredients for Success?
Success in this transformation necessitates collaborative endeavors involving all relevant stakeholders: from researchers, industry practitioners, policymakers, and consumers.
A future with ubiquitous rare earth recycling involves innovation, promoting sustainable practices, and a move to more responsible consumption. Only then “we can collectively work towards a more circular and resilient economy that values the sustainable utilization of critical resources like REEs.”
Final Thoughts
With valuable rare earth elements (REEs), electronic waste (e-waste) could emerge as a sustainable resource management paradigm. The authors in this paper afford an overview of the occurrence of REEs in e-waste, introducing both recovery-focused conventional and emerging green. What are the conventional methods? physical separation, hydrometallurgy, and pyrometallurgy. What about innovative processes ushering in novel innovation? bioleaching, supercritical fluid extraction, ionic liquid extraction, and lanmodulin-derived peptides bring improved environmental sustainability and efficiency.
Offering valuable information in the form of case studies and comparisons concerning the extraction of REEs from waste permanent magnets and fluorescent powders, the authors point to the need for more research and development, focusing on the development of eco-friendly leaching agents, separation materials, and process optimization to bolster sustainability and efficiency involving REE recovery from e-waste. Both sustainable resource recovery and environmental concerns must be top of mind.
The authors are affiliated with the following:
- Ganzhou Key Laboratory of Mine Geological Disaster Prevention and Control and Ecological Restoration, School of Resources and Civil Engineering, Gannan University of Science and Technology
- Chongyi Green Metallurgy New Energy Co., Ltd.,
- School of Minerals Processing & Bioengineering, Central South University, Changsha
Source: Molecules (opens in a new tab)
Daniel
You Might Also Like…